工业文明的演进史,本质上是人类突破生产范式束缚的历史。当福特汽车宣称“顾客可以选择任何颜色的汽车,只要它是黑色的”时,大规模标准化生产代表了制造业的巅峰成就。而今天,消费者在线定制专属汽车配置后数周即可交付的常态,则标志着制造业的核心矛盾已从效率优先转向了个性化需求与规模化生产的内在冲突。这一根本性转变,正在由融合了人工智能视觉检测的柔性制造系统引领突破,开启智能制造的新纪元。
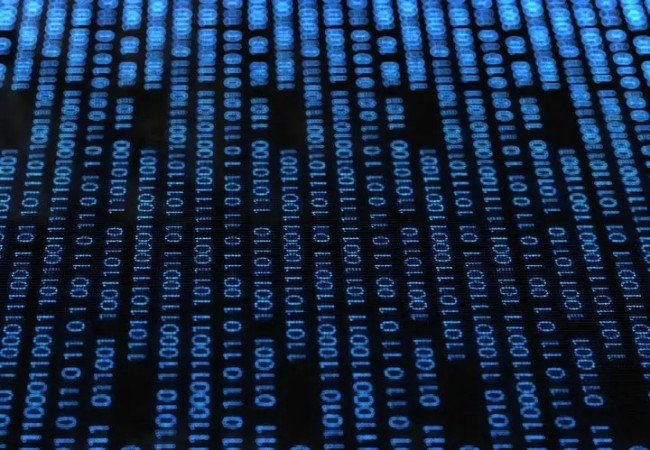
柔性制造系统作为智能制造的“灵活脊梁”,其核心价值在于解决多品种、变批量生产的动态适应性问题。传统刚性产线依赖专用设备和固定节拍,而现代FMS通过数控机床、工业机器人、自动化物料搬运系统及计算机控制系统的深度集成,实现了“不停机快速转换”的三维度柔性化,即产品柔性支持跨品类生产、产量柔性适应订单波动、扩展柔性便于系统功能升级。这种能力本质上重构了生产逻辑——从“以设备为中心”的批量导向,转向“以数据驱动”的需求导向。
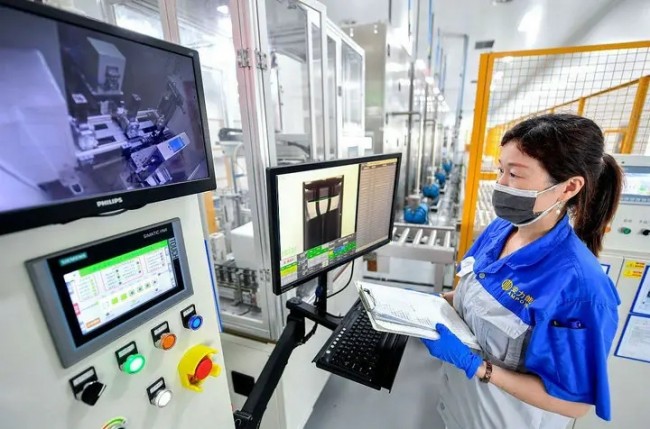
在个性化定制场景中,产品变异性的激增对质量保障体系提出严峻挑战。传统人工检测在效率、一致性和精度上的瓶颈,被AI视觉检测技术彻底突破。它能通过高分辨率工业相机获取产品表面及结构特征,结合深度学习算法实现毫秒级缺陷识别与分类。在精密制造领域,虚数科技研发的DLIA视觉检测系统,已经得到实践验证。在某冲压智能工厂,DLIA视觉检测系统覆盖原材料下料、冲压、焊接到装配全流程,替代人工实现精准品控,使生产过程数据实时集成至中央控制室,关键指标如设备稼动率、合格率实现可视化监控,将漏检率降至0.01%以下,更通过对质量大数据的分析反向优化工艺参数,形成“检测-反馈-修正”的闭环控制。
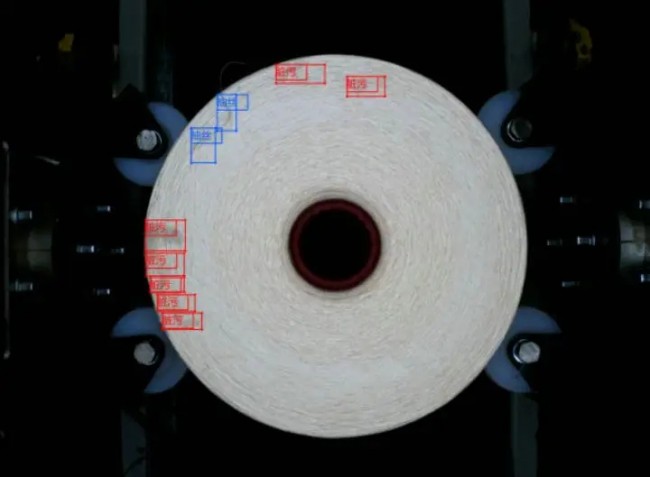