上海光明乳业股份有限公司于2019年6月在我司定制了主旋转盘为32工位的定点定位回转贴标机,目前已经通过验证投入生产线。在传统回转贴标机原则上,一台被设计为回转式的现代化贴标机的结构主体总是不相同的,这些贴标机的贴标速度及定点定位指向能力较高,以牛奶灌装速度和自动化生产线的传输速度每小时的玻璃瓶或容器数量计,原有回转贴标机它们由一个转台6个工位组成,转台的外缘上安装着转盘,在贴标期间接纳容器定向贴标。
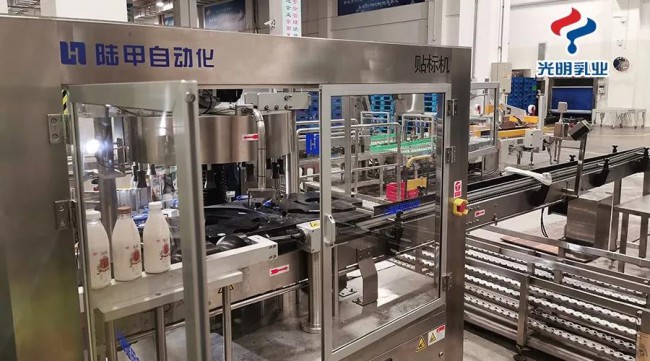
回转贴标机除转台外,贴标机还有让玻璃瓶、PE瓶等被贴物品通过旋转星轮进入贴标机和从贴标机中出来的输入-输出传送带,围绕机器的一个或多个标签分配器将标签由一个辊子或一个长标盒送往贴标站进行精确贴标,压瓶头从上部将瓶子或容器压在托瓶转盘上,使其在高速转动时不会跌倒。通常情况下,现代化贴标机的托瓶转盘采用分散式伺服驱动器。
由于托瓶转盘的位置不断变化,贴标机生产厂家不能安装固定的凸轮,只有使用适时伺服技术才能确保贴标机的高度灵活性。为了准确定位标签,贴标机必须让待贴标容器转动到相应位置,为此需要一个机构或传感器来确定标签在瓶子上的准确位置,它可以是一条接缝或一个标记。传感器识别标记,并将信息发送给上一级的伺服系统,由此实现托瓶转盘的准确定位。
根据要求的定位策略
回转贴标机解决方案,贴标机通过一个机械装置将待贴标容器放到特定位置上,例如通过一个机械凸轮转动待贴标的瓶子,直到瓶底部或瓶侧面的一个接缝或标记嵌入机械制动装置为止。
这意味着更换瓶型或其它包装物时机械成本会很高,因为如果对准缝发生变化,对准单元就必须整个更换,在最坏的情况下甚至还包括机械凸轮。
只有待贴标容器的类型基本不变,对灵活性的要求也不太高时,使用机械对准才有意义。
使用传感器和光线感应器的解决方案
这种贴标机根据需要的位置通过传感器对准待贴标容器,机器上部的光线感应器扫描容器上的接缝或标记,然后将其位置发送给上级控制器。在机器的上部安装传感器是必要的,因为托瓶转盘在进瓶和出瓶星轮下面运行,而这里并没有安装传感器的空间。实际上传感器与在自己前面采用固定速度转动的待贴标容器一起移动。
如果需要传感器寻找瓶子上的特定标记,就使用带有数字输出的传感器,它们可以直接与分散式伺服控制器连接,瓶子在传感器前面转动,传感器识别标记,发出信号,相连的伺服装置在固定的平台内达到零转速,瓶子由此被准确定位。
如果贴标系统根据瓶子或容器上的标记或图案工作,机器中可以使用带有模拟输出的传感器,它也可以直接与分散式伺服控制器连接,与上述系统类似,托瓶转盘会将待贴标容器在随同旋转的传感器前面定位展开。
如果传感器检测到以模拟信号形式出现的标记,伺服装置会再次回到零转速。与数字输出不同的是,为了识别模拟传感器,分散式伺服驱动器中的标记信息必须是已知的。不过这种方式有一个明显的缺点:生产开始前,操作者必须对系统中针对相应瓶型的所有传感器进行校准,这需要时间,而且出错率会升高。
准确和快速:分散式伺服驱动器中的图案
另一种的方式是,直接在伺服驱动器中确定模拟标记信息,由于在分散式伺服驱动器中凸轮的特征十分分散,系统可以储存模拟数据的信号序列用于曲线数据内的特定图案。
更换品种时,用户只需要一次性创建用于新图案的数据,然后传递给系统中的所有分散式伺服驱动器,这样就缩短了切换时间,明显降低了出错率,从而大幅度节约了成本。
另一个方面是识别标记期间整个系统的时间情况,在此重要的是传感器直接与分散式伺服驱动器相连,对于一台贴标能力为36000瓶/每小时的36工位贴标机而言,可用于对准过程的时间大约为225ms。机器在这个时间内必须找到标记,然后通过分散式伺服驱动器进行准确定位。
自动化生产线集成摄像系统
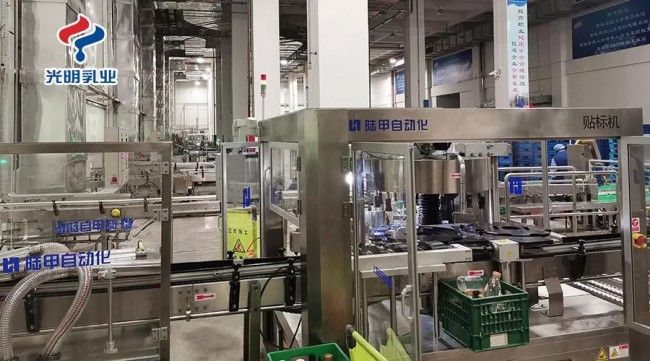
现代化全自动贴标机可借助摄像系统完成瓶对准,与传感器方案不同,摄像系统是固定安装的,在实践中多个摄像机与一个进行图像分析的公共摄像机控制器相连。在这里伺服驱动器也会将转瓶托盘上的瓶子在摄像机前展开,使摄像机能够看到瓶子。
由于摄像系统是固定安装的,因此瓶子经过摄像机的圆形截面比较小,进行识别时摄像机的数量决定了必要的采集角度。使用三个摄像机时,每台摄像机必须采集120°的容器展开角度并将这部分图像发送给摄像机控制器,而不是贴标机的上级控制器。
摄像机控制器将实例中的三个单独图像片段组合成整个展开的全景图片,现在摄像机控制器必须将这一全景图片与参考图像进行对比,这些参考图像是使用者预先通过带有相应标识的容器制作并储存的。摄像系统找到标识,测定修正角度,与参考图像保持一致。
识别标记需要大量的计算工作:一方面控制器必须考虑容器的曲率,这里的难度是:每台摄像机创建一个120°扇面的图像,而不是影像,如果当前容器进入下一台摄像机的视频窗口,下一个容器就会进入之前的摄像机区域,这就需要将图像正确地排列为全景图。
另一方面摄像机控制器必须非常迅速地将修正角度传递给贴标机,让分散式伺服驱动器能够根据事先测定的修正角度进行对准。如今信息大多会直接通过实时以太网传输至相应的伺服驱动器,而不是设备控制器,这样伺服驱动器可以直接进行角度校正。